Table of Contents
In any electrical system, conductors are essential components that carry electrical current from one point to another. Whether you’re designing a simple household electrical system or a complex industrial network, choosing the right conductor material is crucial to the success of your project. The two most commonly used conductors in electrical wiring are copper and aluminum. Each offers unique advantages and considerations depending on the specific needs of your application.
This article explores the key characteristics, benefits, and drawbacks of copper and aluminum conductors, helping you determine which one is the best fit for your next electrical project.
Understanding Conductors: Copper and Aluminum
Conductors are designed to transmit electrical current, and their primary function is to ensure the efficient transfer of electricity with minimal resistance. The selection of conductor material depends on various factors such as cost, conductivity, weight, and flexibility. Copper and aluminum are the most popular choices, and both materials have distinct advantages that make them suitable for different applications.
Copper Conductors
Copper has been the standard material for electrical conductors for centuries. It offers superior electrical conductivity, strength, and durability, making it the ideal choice for applications where maximum efficiency is required. Copper is rated as the benchmark for electrical conductivity, with 100% IACS (International Annealed Copper Standard) serving as the standard of comparison for other conductive materials.
Advantages of Copper Conductors:
- High Electrical Conductivity: Copper is more conductive than most metals, which results in lower resistance and reduced energy loss.
- Durability: Copper is highly durable and resistant to corrosion, ensuring a long lifespan even in challenging environmental conditions.
- Heat Resistance: Copper can withstand high temperatures without compromising its strength or conductivity, making it ideal for applications with high thermal demands.
- Flexibility: Copper conductors are highly flexible, which makes them easy to work with, especially in tight spaces.
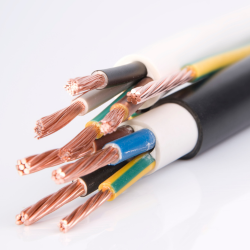
Disadvantages:
- Cost: Copper is generally more expensive than aluminum, which can increase the cost of large-scale wiring projects.
Applications of Copper Conductors:
- Commercial and Residential Wiring: Copper conductors are commonly used in wiring systems for homes, offices, and industrial buildings due to their reliability and high conductivity.
- Power Distribution: Copper is essential in power generation and distribution systems, ensuring efficient transmission of electricity over long distances.
- Automotive Wiring: In the automotive industry, copper is used for wiring, motors, and battery connections due to its excellent conductivity and durability.
- Electronics: Copper is frequently used in the production of electrical components and connectors in various electronic devices, including computers, communication systems, and more.
Aluminum Conductors
Aluminum conductors are an economical alternative to copper. Although aluminum has lower electrical conductivity than copper, it offers significant cost savings and is well-suited for certain applications where weight is a critical factor.
Advantages of Aluminum Conductors:
- Cost-Effectiveness: Aluminum is much cheaper than copper, making it an ideal choice for large-scale projects that require significant amounts of wiring, such as power transmission lines and large infrastructure projects.
- Lightweight: Aluminum is significantly lighter than copper, making it easier to transport and handle, particularly in large installations or overhead power lines.
- Flexibility: Aluminum conductors are flexible, making them easier to work with during installations, especially when large volumes of wire need to be deployed.
- Corrosion Resistance: Aluminum is resistant to corrosion in certain environments, such as in saltwater, which is why it’s commonly used for marine and offshore electrical systems.
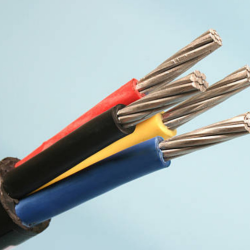
Disadvantages:
- Lower Conductivity: Aluminum’s electrical conductivity is lower than copper’s, meaning larger conductors are required to carry the same amount of current, which can make it less efficient in some applications.
- Vulnerability to Vibration: Aluminum is more prone to damage from vibration compared to copper, which can be a concern in certain applications like high-speed machinery.
- Oxidation: While aluminum has corrosion-resistant properties, the surface of aluminum conductors can oxidize, which may increase resistance and cause connection issues over time. Special care must be taken to ensure proper connections and to avoid overheating.
Applications of Aluminum Conductors:
- Overhead Power Transmission Lines: Aluminum’s cost-effectiveness and lightweight nature make it a popular choice for large-scale power transmission lines, where weight reduction is essential, and copper’s higher cost is not justified.
- Aircraft and Aerospace Wiring: The aerospace industry uses aluminum for wiring in aircraft, where reducing weight is crucial without compromising safety or functionality.
- Automotive Prototypes: In the automotive industry, aluminum conductors are often used in the development of fuel-efficient vehicles due to the material’s light weight.
- Industrial Applications: Aluminum is used for wiring in some industrial applications, where the cost savings from aluminum outweigh the drawbacks of its lower conductivity.
Key Differences Between Copper and Aluminum Conductors
Property | Copper | Aluminum |
Electrical Conductivity | Higher conductivity, minimal energy loss | Lower conductivity, requires thicker wires for the same current load |
Cost | More expensive | More cost-effective |
Weight | Heavier | Lighter |
Durability | More durable, resistant to corrosion | Less durable, prone to oxidation and damage under stress |
Flexibility | Highly flexible and easy to work with | Flexible but less so than copper |
Applications | Best for commercial, residential, and power distribution | Ideal for overhead transmission, aerospace, and large infrastructure projects |
Choosing the Right Conductor for Your Project
The decision to use copper or aluminum conductors ultimately depends on the specific requirements of your project. Here are some key considerations to help you make the right choice:
- Cost: If your project requires a large amount of wiring and budget is a significant concern, aluminum conductors might be the more cost-effective choice. However, if efficiency and long-term performance are top priorities, copper may justify the higher upfront cost.
- Electrical Efficiency: Copper’s superior conductivity makes it the best choice for applications where minimal energy loss is essential. Copper is ideal for power distribution and high-performance electronics where energy efficiency is critical.
- Weight: If reducing the weight of the wiring is important, such as in overhead transmission lines or aircraft wiring, aluminum is the clear choice.
- Durability: If the wiring will be exposed to harsh conditions, such as high humidity or high temperatures, copper’s durability and resistance to corrosion make it the better option.
- Vibration and Mechanical Stress: For environments with significant vibration, copper’s greater resistance to mechanical stress can help ensure the longevity of your wiring.
Conclusion
Both copper and aluminum conductors have distinct advantages, and understanding their properties will help you choose the best conductor for your specific application. Copper remains the top choice for high-efficiency, high-performance applications due to its superior conductivity and durability. However, aluminum offers an affordable alternative for large-scale projects where cost and weight are more significant concerns.
By carefully considering factors such as cost, conductivity, durability, and application requirements, you can make an informed decision and select the conductor that will best serve your needs.
Table of Contents